Elastomers and Rubbers — What's the Difference?
Both "rubber" and "elastomer" are used to describe the makeup of components, fixtures and parts across industries and often seem to describe different things. However, "rubber" and "elastomer" are two ways to describe the same thing — elastomer is a description for any type of elastic material, such as synthetic rubber, while rubber is a specific type of elastomer. "Rubber" is often used as a shorthand description for "natural rubber," which is different from its more common synthetic counterpart.
Learn more about the differences and similarities between elastomers and rubbers to determine which is better for your industry and project.
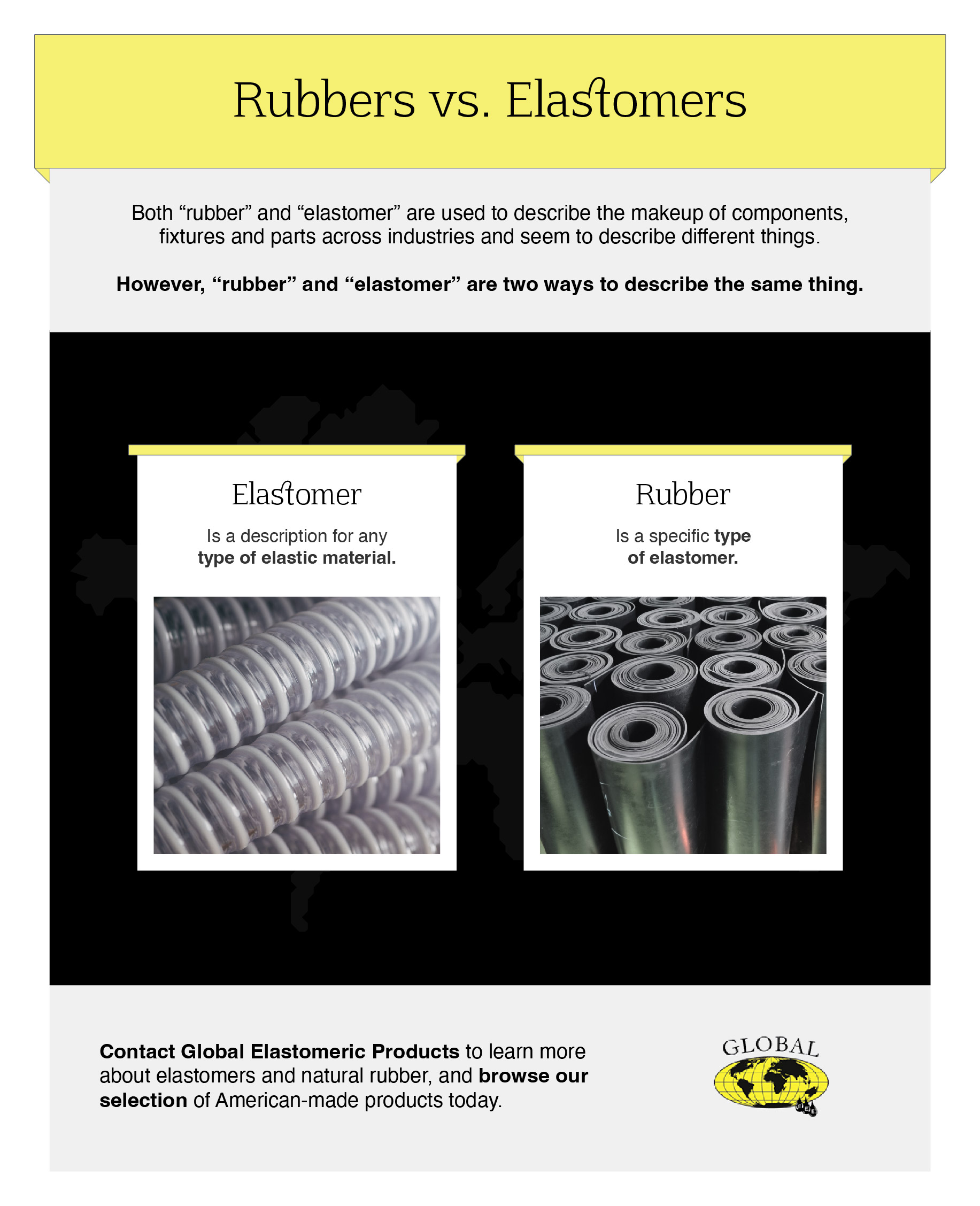
Table of Contents
- What Are Elastomers?
- What Is Natural Rubber?
- Which Material Is Right for Your Project?
- Contact Global Elastomeric Products, Inc. to Learn More
What Are Elastomers?
Elastomers are "elastic polymers," which is how they got their name. They are made of long, coiled polymer chains. These chains begin as monomers until they undergo polymerization, an artificial process that changes monomers into polymers, which stretch when pulled and return to their arrangement when released, producing their elastic properties. Since rubber also has elastic properties, "elastomer" and "rubber" have become interchangeable, though they don't necessarily always refer to the same material.
The polymer chain is linked together by strong covalent bonds that can be further strengthened through processes like vulcanization, also called curing, interlinking or cross-linking. During vulcanization, the bonds holding the polymer chain together are fused with additives such as sulfur that strengthen the connection and make the material more rigid and less susceptible to force and heat. These qualities make some elastomers, particularly thermoset elastomers, a popular choice for parts that need to withstand high temperatures in vehicles, medical equipment and tools.
Common examples of elastomer applications include:
- Industrial moldings
- Tools and appliances
- Lubricants
- Sealants and caulking
- Gaskets
- Industrial drive belts
- Prosthetics
- Consumer products
- Vehicle components
- Wiring and cable insulation
- Medical devices
Elastomer components are manufactured through injection, transfer or compression molding, depending on the application and final product.
Types of Elastomers
Because they're produced synthetically, elastomers can be adapted to fit specific end-uses. Some have superior chemical resistance, while others are designed to withstand harsh environmental conditions. Some common types of elastomers include:
- Thermoset elastomers: These are vulcanized elastomers that do not melt in extreme heat. They're the most commonly used elastomer available.
- Thermoplastic elastomers: These elastomers have weaker cross-links consisting of repeating rigid and soft units, so they can be melted and reformed without losing elasticity. They are recyclable.
- Saturated elastomers: These go through a special vulcanization process that doesn't involve sulfur, making them less reactive and more resilient to environmental conditions, like oxygen, radiation and ozone. Silicone rubber and polyacrylic rubber are two common types of saturated elastomers.
- Unsaturated elastomers: These are any elastomer that can be vulcanized with sulfur, like butyl rubber, chloroprene rubber, polybutadiene and polyisoprene.
Benefits of Using Elastomers
Elastomers are common for industrial materials and manufacturing processes because they are:
- Versatile: Elastomers can be quickly engineered to fit necessary specifications, including size, shape, flexibility and appearance, making them an extremely versatile material compared to metal or plastics.
- Durable: Elastomers are durable when force is applied, such as stretching or pulling. They won't snap or break as quickly as weaker manufacturing materials.
- Resistant: Elastomers are highly resistant to abrasion and environmental conditions. They withstand high temperatures without losing their structural integrity or changing appearance, and they won't break down during long-term exposure to flames. They can withstand shock, making them ideal for mining and electrical applications, and they can be engineered to resist or conduct electricity as needed. The structural strength keeps liquids, gases and air inside and protected in all applications.
- Insulating: Many elastomers — like elastomeric foam, found in many HVAC and refrigerant units — are used for industrial level insulation against extreme heat or cold. They are ideal for settings where other materials might break or become otherwise compromised.
Things to Consider Before Using Elastomers
Using a synthetically engineered elastomer can be very beneficial for a range of products and industries, as long as you consider the following:
- Temperature limits: Though highly resistant, each type of elastomer has a temperature limit. If it gets too cold, it could get brittle or become too rigid to stay flexible. If the elastomer isn't damaged, extreme cold is usually reversible without permanent consequence. However, if an elastomer gets too hot, it undergoes permanent chemical changes, which could be detrimental in applications like gaskets and seals.
- Fluid compatibility: Elastomers must be compatible with any fluid they contain or contact. Fluid compatibility depends on the type of elastomer and fluid, its rigidity, the fluid's temperature, how long the elastomer is exposed and other factors. Some elastomers are also rated as poorly, moderately or highly resistant to oil.
- Disposal after use: Unlike natural rubber, synthetic elastomers are not biodegradable, and many additives are too toxic for organic decomposition. Dispose of synthetic elastomers at rubber recycling facilities or reuse materials. Recycled rubber is repurposed into many things, such as playground surfacing, doormats, garden mulch and sports turf, and can be used to stabilize concrete sidewalks and roadways.
What Is Natural Rubber?
Natural rubber is a type of elastomer, an organic compound and an isoprene polymer made directly from nature. Many plants — most commonly the Hevea brasiliensis tree, but also rubber fig and Pará rubber trees — contain a natural, white and sap-like substance called latex, which is harvested, processed and used for multiple applications. Most natural rubber comes from Thailand, but other Asian countries have also started producing natural rubber from various plant sources.
As of 2019, 13.804 million tons of natural rubber were produced worldwide, and experts expect that number to increase. Compared to the long, randomized polymer chain in synthetic elastomers, natural rubber consists of loosely joined, tangled isoprene monomers that can be pulled apart and altered but will still revert to their original shape when the force is removed. This gives it the natural flexibility and elasticity rubber is known for.
Natural rubber is softer than synthetic rubber and other elastomers, making it better for things like:
- Anti-vibration components
- Springs and bearings
- Rubber bands
- Rubber cement mixtures
- Adhesive materials
- Automotive parts
- Industrial hoses
- Shoe soles
- Soil stabilization
- Medical tubing
- Latex products
The majority of natural rubber is used for high-performance tires because it's strong and heat resistant.
Types of Rubber
Natural rubber is not a category — it's a specific variation of elastomer. There is only one type of natural rubber, though it can be sourced from several different plants and countries and adapted to fit various industry applications. Aside from natural rubber, other types of elastomers labeled as rubber include:
- Nitrile rubber: This is a commonly used rubber with good fluid resistance, perfect for industrial and manufacturing applications, like seals. It's highly resistant to fuels, oils and alcohol. One of the most common nitrile rubber applications is disposable gloves.
- Ethylene propylene diene monomer rubber: This type of rubber is resistant to heat, environmental wear and natural aging. It is usually used as a more affordable alternative to silicone because it's long-lasting and suitable for electrical use.
- Butyl rubber: This rubber type absorbs shock and is durable against moisture, heat, chemicals and abrasion. It's often used for electrical insulation and sealants.
- Hydrogenated nitrile rubber: Compared to standard nitrile rubber, hydrogenated nitrile rubber is more resistant to extreme heat, chemicals, hot water, steam and fuels. It's very strong and abrasive-resistant but isn't suitable for electrical insulation or organic solvents.
- Chloroprene rubber: This rubber, more commonly known as Neoprene, is oil- and flame-resistant. It's used for seals, coating fabrics and some medical equipment and bracings.
- Epichlorohydrin rubber: This rubber is resistant to acids and ozone but isn't suitable for sealing applications and could corrode metals and metal-bonded parts.
- Fluorosilicone rubber: Though not as cost-efficient as other types of rubber, fluorosilicone resists high temperatures and ozone and is resilient against electrical currents.
Benefits of Using Natural Rubber
What is rubber used for? Natural rubber is the optimal choice for many applications because it is:
- Biodegradable: Natural, unaltered rubber is plant-derived, which makes it biodegradable. Any additives, curing materials or filler will render natural rubber nonorganic and unable to decompose safely or naturally.
- Sustainable: Natural rubber derived from latex is renewable, making it more sustainable than synthetically produced rubber.
- Consistent: Since rubber is derived from latex, a naturally occurring material, it has consistent, set monomers that do not vary as much as synthetic rubber does. This consistency makes it easy to predict and work with across applications.
- Flexible: Natural rubber is one of the most flexible types of rubber, with high resistance to tearing and the ability to return to its natural form after force is applied.
- Adhesive: Latex sap is naturally sticky, and when environmental conditions manipulate natural rubber, it can become tacky and show characteristics of its former state. This makes natural rubber a good choice for many types of adhesives.
- Nonreactive: In its natural state, rubber is less chemically complex than synthetic variations, making it less reactive to many fluids, gases and chemicals than synthetic elastomers. This less reactive state makes it safer and more predictable to work with than synthetic elastomers.
Things to Consider Before Using Natural Rubber
Natural rubber is a sustainable, consistent and nonreactive alternative to synthetic materials, but it's not the right fit for every application. Consider the following:
- Temperature changes: Temperature monitoring is crucial with natural rubber. It becomes tacky and more pliable if it gets too warm, while extreme cold could cause it to crystallize and become too rigid.
- Production cost: Though sustainable and renewable, latex and natural rubber do not replenish themselves overnight. Because of this, it's not always widely available, and the price tends to fluctuate.
- Fillers and additives: Natural rubber is sometimes combined with filler products, like carbon black or silica, making it more stable and resistant to environmental conditions. Consider all additives in the application and whether they alter the rubber's natural state or if additives are synthetic.
- Substance resistance: Because it's plant-derived, natural rubber has weak resistance to grease, fats, oils and ozone, which can disintegrate some components.
- Latex allergies: Natural rubber is generally nontoxic and free of hazardous substances, like petroleum, but it's derived from latex, which some people are allergic to. Although rare, latex reactions occur upon skin contact and can render some products unsafe for use.
Which Material Is Right for Your Project?
Using an elastomer material that is too weak could result in damaged products, safety hazards or equipment breakdown. Using a rubber that's too strong for your chosen application could render it unusable or too rigid to fit your project's changing needs. If you're sourcing materials for an upcoming manufacturing project or selecting the best seal and gasket type for your work site, consider these factors:
- Temperature: Consider your project's temperature range, including the lowest and highest possible temperatures and the length of exposure to those temperatures.
- Substances: Note all substances the rubber will come into contact with internally and externally. Will exposure be occasional, unlikely or constant? Possible substances include chemicals, cleaning agents, water, ozone, gases, grease, oil, fats and flames. Many elastomers can be altered with additives and synthetic filler that can help them resist otherwise harmful substances.
- Duration: How long will the rubber component be in place? Rigid, resistant materials are critical for safe and effective long-term use.
- Availability: Whether naturally derived or synthetically produced, material availability affects everything from production time and delays to the total cost of supplies and equipment.
- Industry: Each industry has standards for material selection based on efficacy, safety and manufacturing regulations. Use the recommended rubber type for your chosen industry and application and always work within compliance.
Using the right elastomer is critical for protecting your bottom line and managing operating costs. For example, if you need a heat-resistant elastomer and automatically select the most heat-resistant material available, it may not be the most economical decision when a lower-cost alternative could have provided the same level of protection and efficacy.
Contact Global Elastomeric Products, Inc. to Learn More
Elastomers are elastic polymers, typically infused with synthetic materials and produced to fit specific applications, industries and projects. Natural rubber is one type of elastomer — a flexible, naturally-derived substance produced from latex sap. Both elastomers and natural rubber are highly versatile materials and offer endless possibilities in manufacturing and product design. Depending on the type you choose, rubber parts can be extremely resistant to abrasive substances, extreme temperatures and environmental wear.
Global Elastomeric Products, Inc. is an ISO-certified company specializing in oilfield and agricultural rubber products. All products are guaranteed free of defects, backed by 50 years of industry experience and attentive customer service to help you make the right investment for your project. Our team is here to help with any project, no matter the size or application, with quick turnaround times throughout the design and implementation process.
Contact Global Elastomeric Products to learn more about elastomers and natural rubber, and browse our selection of American-made products today.